The Hidden Costs of Poor Inventory Management
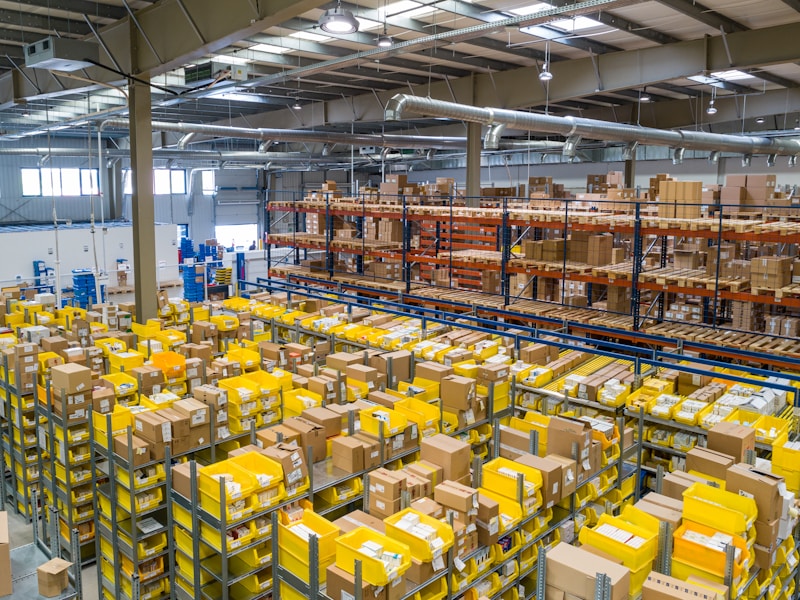
Most facility managers know they're losing money on inventory, but few realize just how much. The true cost of poor inventory management goes far beyond the obvious waste of over-ordering or emergency purchases.
Consider what happens when a critical HVAC filter isn't in stock during a routine maintenance check. The technician can't complete the job, so they move on to other tasks. The equipment runs with a dirty filter, reducing efficiency and potentially causing damage. A week later, when the filter finally arrives, you're paying for another service call, plus the energy waste from the dirty filter, plus potential equipment damage. What should have been a $20 filter replacement becomes a $200+ problem.
Smart inventory management systems eliminate these cascading costs by maintaining optimal stock levels automatically. They track usage patterns, predict needs based on maintenance schedules, and can even integrate with vendor systems for automatic reordering. This isn't just about having parts when you need them—it's about having exactly the right amount at exactly the right time.
The facilities teams that have mastered inventory management report 30-40% reductions in total inventory costs, not through cutting corners, but through eliminating waste and inefficiency. When every part has a purpose and every purchase has a plan, your inventory becomes a strategic asset rather than a necessary evil.